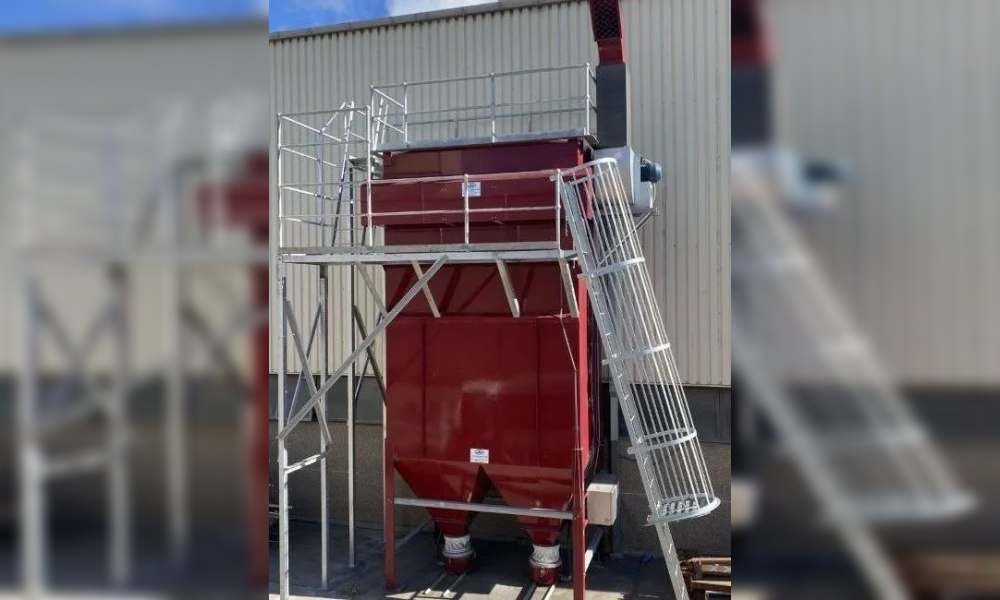
Understanding Different Types of Dust Extraction Systems
In environments like manufacturing plants, construction sites, and metal workshops, managing dust is more than just a matter of cleanliness. Dust extraction systems play a pivotal role in ensuring worker safety, preserving equipment, and staying compliant with air quality standards. Yet, with the variety of extraction systems available, it’s easy to feel overwhelmed when choosing the right one for your workplace.
Why Dust Extraction Matters
Why all the fuss about dust? Well, dust in industrial environments can lead to severe health issues, compromise machinery, and even result in costly downtime. Poor dust management also puts facilities at risk of regulatory penalties if air quality standards aren’t met.
So, the right dust extraction system isn’t just beneficial—it’s essential. The right system can capture fine particles, mitigate fire risks, and protect employees from respiratory hazards.
Types of Dust Extraction Systems
Dust extraction systems come in various forms, each designed for specific types of dust and operational demands. Let’s explore the primary types to see what each has to offer.
1. Cyclone Dust Collectors
Cyclone dust collectors operate using centrifugal force to separate heavier particles from the airstream. Dust-laden air enters the system and spins in a cyclonic motion, which pushes larger dust particles to the walls of the collector. These particles then slide down into a collection chamber, while the cleaner air moves on to additional filtration or exhausts out of the system.
- Where They Excel: Great for handling large, coarse dust particles like sawdust or metal shavings.
- Best For: Woodworking shops, manufacturing floors, and metal grinding applications.
- Considerations: Cyclone dust collectors may need additional filters to capture fine dust, as their primary strength is removing heavier particulates.
2. Reverse Pulse Dust Extractors
Reverse pulse dust extractors are well-suited for applications requiring thorough dust filtration. This system uses filter cartridges to capture dust, which builds up on the filter surface over time. A reverse pulse of compressed air periodically cleans the filters, forcing dust into a collection bin and preventing filter clogging. The pulse cleaning ensures consistent filtration and maximises airflow, making it an excellent choice for high-dust environments.
- Where They Excel: Perfect for capturing fine dust and particulates, particularly in settings with high dust generation.
- Best For: Industries like mining, cement, welding, and pharmaceutical production where continuous, efficient dust collection is critical.
- Considerations: Regular maintenance is required to keep compressed air lines clean and ensure pulse function efficiency. However, these systems are robust, long-lasting, and maintain peak performance with consistent cleaning.
3. Cartridge Dust Collectors
Cartridge dust collectors, known for their compact design, capture fine dust using high-efficiency filter cartridges. These filters trap particles on their surface, allowing for easy cleaning and reusability. Often, these systems also use compressed air to clean the cartridges, making them effective for removing fine dust from the filter surface. The result is a powerful, space-saving dust extraction solution.
- Where They Excel: Ideal for capturing fine, lightweight dust, such as welding fumes or pharmaceutical powders.
- Best For: Laboratories, electronics manufacturing, and any environment where fine dust control is a priority.
- Considerations: Cartridge collectors require regular cleaning to avoid clogging, particularly in high-dust areas.
4. Baghouse Dust Collectors
Baghouse dust collectors are one of the most popular choices for high-volume dust collection. These systems use large fabric bags to filter dust particles from the air, allowing both large and small particulates to be effectively captured. Dust particles accumulate on the bag’s surface, which is periodically cleaned to maintain filtration efficiency.
- Where They Excel: Extremely effective at handling both large and fine particulates.
- Best For: High-dust industries such as cement manufacturing, foundries, and chemical plants.
- Considerations: Baghouse systems can be bulky, and the bags require periodic replacement to ensure continued effectiveness.
5. Wet Scrubbers
Wet scrubbers use a water or liquid mist to capture dust particles, making them excellent for applications involving explosive or combustible dust. In a wet scrubber, dust-laden air passes through the mist, and particles get trapped in the liquid. These particles are then directed to a settling chamber for disposal, which significantly reduces dust in the air.
- Where They Excel: Excellent for handling hazardous dust that could ignite or explode.
- Best For: Foundries, chemical processing plants, and metalworking environments.
- Considerations: Wet scrubbers require careful wastewater disposal and may need special measures to meet environmental standards for emissions.
Deciding Which System is Right for You
So, how do you choose the best dust extraction system for your specific needs? Here’s a quick guide to help narrow down your options.
- Dust Type: Are you dealing with coarse particulates or fine dust? Systems like cyclones excel at capturing large particles, while cartridge or reverse pulse extractors work well for finer dust.
- Volume of Dust: High-dust environments, like cement plants or metal workshops, benefit from heavy-duty systems like baghouses or reverse pulse dust extractors.
- Health and Safety Compliance: Industries with strict air quality standards might need advanced filtration, such as cartridge systems or wet scrubbers.
- Space Requirements: Baghouse systems require ample space, whereas cartridge systems are more compact and can fit into tighter spaces.
- Maintenance Needs: Reverse pulse and cartridge collectors require regular cleaning to maintain airflow, while cyclone systems need minimal upkeep.
The Right Choice Makes All the Difference
Choosing the right dust extraction system is not only about meeting operational needs but also about prioritising worker safety and regulatory compliance. Whether it’s the continuous pulse cleaning of a reverse pulse extractor or the simplicity of a cyclone system, each type has its strengths. The best choice will depend on your specific dust type, facility layout, and how much maintenance you’re willing to commit to.
Take time to assess your unique requirements. A well-matched dust extraction system will improve air quality, extend equipment life, and provide a safer work environment for everyone involved.