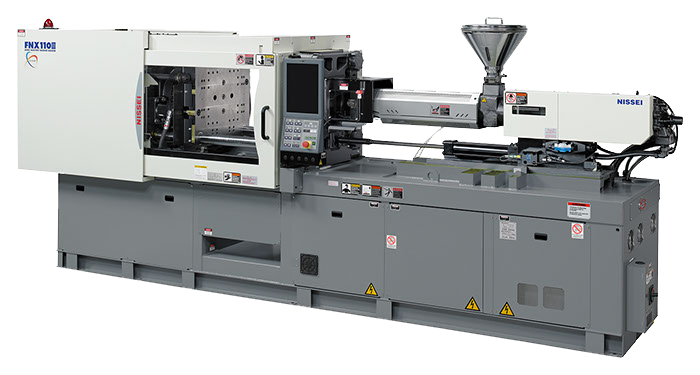
How to Ensure Quality Control With Your Plastic Injection Mold Maker
Quality control is an essential part of any manufacturing process. It allows you to ensure that your products work correctly and meet your customers’ needs. Injection molding is no exception to this rule.
Check the Quality of the Materials
Ensure that the materials used in your mold maker are of high quality. This will save you time and money in the long run.
The resins poured into the plastic injection mold makers must meet specific criteria. These include tensile strength, chemical resistance, durability, and more.
These requirements will determine which thermoplastic resins are best for your project. For example, PMMA, acrylic, and ethylene-propylene rubber are all suitable for specific applications.
Once your materials have been chosen, they must undergo tests and inspections to meet these requirements.
In addition to visual inspections, inspectors may also test the parts for functionality. They will look for issues like burn marks and other problems caused by poor production quality.
Check the Quality of the Mold
Getting a suitable mold made is vital for creating quality plastic products. It is the part that will hold molten plastic to create a final product, and it must be of the right size and shape for the intended use.
If the mold isn’t fabricated to your specifications, it can lead to many problems. You’ll need to look for a company that follows stringent standards and has proper inspection procedures.
A good mold maker will ensure the parts fit well together before they start the injection molding process. This ensures no problems with the molded product when it comes out of the mold.
Another issue to watch out for is flash, which occurs when molten plastic escapes the cavity and leaves extrusions that stick to the product.
These are a natural part of the injection molding but can indicate low production quality. Luckily, good design can often hide these, but you’ll want to watch for them.
Check the Quality of the Parts
When working on a new project, you must ensure that your parts are made from high-quality materials. This will help you to avoid manufacturing problems during production.
When it comes to quality control, there are a few things that you should look out for when checking the parts that your plastic injection mold maker uses. These include flow marks, weight, surface finish, gate appearance, and deformations.
Injection molded parts often contain ribs and bosses that serve as points for attachment or assembly. They also have holes designed to accommodate screws and threaded inserts.
Injection molded parts can also have sink marks, which occur when the plastic shrinks more in thicker areas than in thin ones. This results in a depression on the wall adjacent to the part. It’s essential to check your ribs and bosses for these sink marks before placing them in your mold. These defects can lead to costly issues when it comes time to produce the parts.
Check the Quality of the Packaging
Quality control is a crucial part of the plastic injection mold maker process. It ensures that your parts are manufactured to the specifications you need and allows for early detection of any issues.
Injection molding is a manufacturing process that uses a machine to melt plastic pellets and push them into a cavity in a mold. The melted plastic then cools and shrinks back to its original shape.
It is essential to remember that the designing, prototyping, building, and testing phases can take months to complete.
A good plastic injection mold maker will have an in-house tool room with access to various tooling materials and machines. A quality mold maker will also be able to provide you with first-article inspection reports, which help identify any issues that might affect your product.