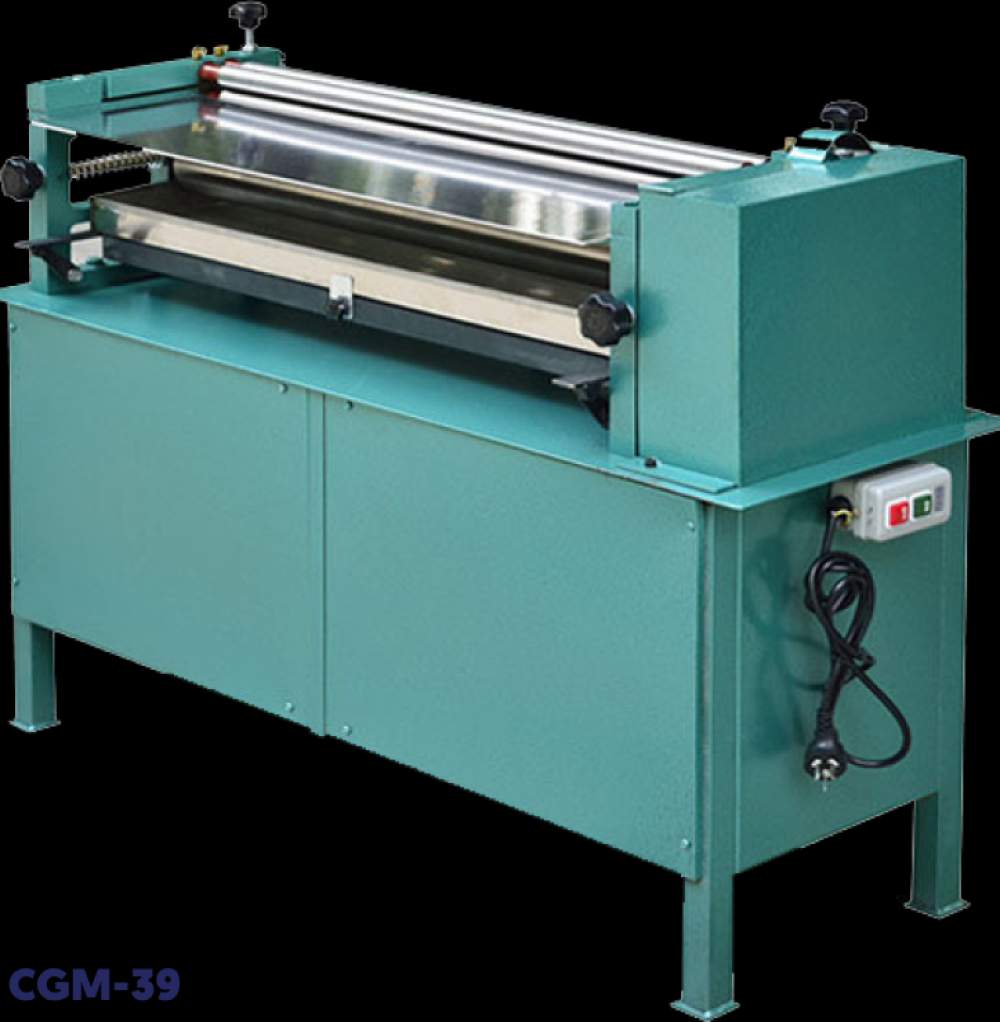
Cold Glue vs. Hot Melt: Advantages of Industrial Cold Glue Machines
Picture this: a bustling industrial facility where packaging and labeling are at the heart of every operation. It’s a world of precision and efficiency, where every choice can make a significant impact. In this dynamic setting, the choice between cold glue and hot melt adhesive isn’t just a mundane decision—it’s a pivotal one. Let’s find out why an industrial cold glue machine makes more sense.
The Sticky Situation: Cold Glue vs. Hot Melt
Before we delve into the perks of cold glue, let’s quickly understand the fundamental difference between cold glue and hot melt adhesive systems.
- Cold Glue: As the name suggests, cold glue adhesive is applied at room temperature. It’s water-based and non-toxic, making it environmentally friendly. This type of adhesive is often used for labeling bottles, cartons, and other packaging materials.
- Hot Melt: Hot melt adhesive, on the other hand, is applied in a molten state and solidifies as it cools. While it’s widely used for sealing boxes and other packaging applications, it comes with its own set of challenges, which we’ll explore shortly.
The Advantages of Industrial Cold Glue Machines
1. Eco-Friendly and Non-Toxic
One of the standout advantages of cold glue adhesive is its eco-friendliness. Unlike hot melt, cold glue doesn’t release harmful fumes during application. It’s water-based, which means it’s non-toxic and safe for both the workers handling it and the environment. So, when you opt for cold glue, you’re making a responsible choice that doesn’t compromise on safety.
2. Lower Operating Costs
In today’s competitive industrial landscape, cost-efficiency is a top priority. Cold glue systems shine in this department. They require less energy to operate than hot melt systems, which need to maintain a high temperature to keep the adhesive in a liquid state. This translates to lower electricity bills and reduced operating costs over time.
3. Better Adhesion and Quality
When it comes to ensuring that labels and packaging materials stay put, cold glue excels. It provides excellent adhesion to various surfaces, including paper, cardboard, glass, and plastic. This means your labels won’t peel off or get damaged easily during transit, ensuring that your products arrive in pristine condition.
4. Easy Cleanup and Maintenance
Imagine a scenario where you need to shut down your production line for hours to clean up adhesive spills and residue. With cold glue, such nightmares are a thing of the past. It’s water-soluble and easy to clean, reducing downtime and maintenance hassles. This keeps your production line running smoothly and your team stress-free.
5. Versatility in Application
Cold glue systems offer versatility in application. They can handle a wide range of packaging materials and product types. Whether you’re labeling bottles, cartons, or packaging food products, cold glue machines can adapt to your specific needs without a hitch.
6. Improved Worker Safety
Safety should always be a priority in any industrial setting. Cold glue adhesive enhances worker safety by eliminating the risk of burns associated with hot melt systems. With cold glue, there’s no need to handle scalding hot adhesive, reducing the chances of accidents and injuries.
7. Reduced Environmental Impact
In an era where sustainability matters more than ever, cold glue adhesive shines as an environmentally responsible choice. Its water-based nature reduces the carbon footprint associated with adhesive production and disposal. By opting for cold glue, you’re contributing to a greener and cleaner planet.
8. Consistency in Application
Consistency is key in the world of packaging and labeling. Cold glue machines offer precise and consistent adhesive application, ensuring that every label or package gets the same quality treatment. This consistency is vital for maintaining the professional look of your products.
Overcoming Common Challenges with Cold Glue
While we’ve highlighted the numerous advantages of cold glue machines, it’s important to acknowledge that no system is without its challenges. However, the good news is that most of these challenges can be easily overcome with proper planning and maintenance.
1. Temperature Sensitivity
One of the primary concerns with cold glue is its sensitivity to temperature. In colder environments, the adhesive can become thicker and less fluid, affecting its application. To tackle this issue, many cold glue systems come equipped with temperature control mechanisms. Ensuring that the adhesive remains at an optimal temperature can help maintain consistent application even in varying climate conditions.
2. Drying Time
Compared to hot melt adhesives that solidify quickly, cold glue may have a longer drying time. This can lead to the need for additional curing or drying equipment in your production line. However, with proper planning and adjustments to your workflow, you can mitigate this challenge. Some cold glue machines offer adjustable drying times to better match your specific requirements.
3. Adhesive Selection
Selecting the right type of cold glue adhesive is crucial to ensure it adheres effectively to your packaging materials. Different substrates may require different formulations of cold glue. Working closely with adhesive suppliers and conducting compatibility tests can help you identify the best adhesive for your needs.
Conclusion
From its eco-friendliness and cost-efficiency to its superior adhesion and worker safety, cold glue machines are a solid choice for your industrial adhesive needs.
So, the next time you’re faced with the sticky situation of choosing an adhesive system, consider the advantages of industrial cold glue machines. Make the switch to cold glue, and watch your packaging and labeling endeavors stick with success.