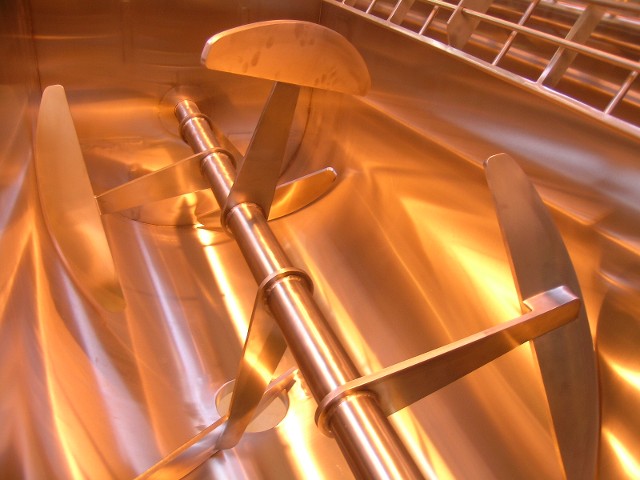
How an Industrial Blender Can Improve Nutraceutical Quality Control
Whether you’re looking to improve the quality of your food, drug, or other product, an industrial blender can help. Blenders are a key component in many production processes, especially for powders and other dense materials.
They can make a big difference in the overall blending process by increasing consistency and efficiency. If you need an industrial blender, check out this article to learn how it can benefit your company.
Improved Product Quality
In most contemporary manufacturing, a blender is essential. This device allows people to calculate the proportions needed for a certain product and scale the ingredients up to the blender’s capacity.
These industrial blender for nutraceuticals are large tanks that mix and blend batches of manufacturing materials to create a reaction between the components. They are also used in scientific operations that require mixing chemicals and medications.
These specialized machines can produce mixtures that may take people hours to mix by hand. Moreover, industrial blenders are economical and are often a key tool in modern production endeavors.
Industrial blenders make coffee beans, spices, seasonings, flour, tea powder, and frozen foods in the food industry. They also are used in the chemical and pharmaceutical industries to mix and emulsify dry solids.
Reduced Waste
Blenders are essential for many industries, including food, pharmaceuticals, chemicals, and cosmetics. They create emulsions, reduce particle size, complete chemical processes, modify material flow, and dissolve components.
A wide range of industrial blenders are available, all designed and constructed to meet the demands of certain applications. The right one for your application is often found by asking a knowledgeable team to assist you in selecting the right machine for your needs.
Generally, the capacity of an industrial blender is determined by its container’s size. The container’s size will determine how much product you can mix at a time and how many steps are required to get your product ready for use.
Increased Efficiency
Many modern manufacturing processes require the mixing of multiple materials. This can include liquids, granules, salts, powders, and other materials with different consistencies.
Industrial blenders mix and blend these diverse raw materials into one mixture for a particular process. They can be used in various industries, including the chemical, agricultural, pulp and paper, pharmaceutical, water treatment, and automotive industries.
The main advantage of an industrial blender is that it can be scaled up to handle large amounts of mix. This capacity allows people to calculate the correct proportions needed for a certain product and mix it up in less time than a normal blender.
An industrial blender can improve nutraceuticals’ quality by mixing the ingredients to create a smooth and consistent texture. In addition, it can also help reduce waste because it can mix the components without the use of toxic chemicals or additives.
Reduced Downtime
In most powder-processing industries, mixing and blending are essential to manufacturing products. These processes are used for various products, including food, pharmaceuticals, metal powder, and chemical ingredients.
Often, these processes involve using ribbon mixers, which take up significant space in a manufacturing facility. This is especially true for large-scale operations, and these machines’ cleaning and maintenance costs can increase quickly.
These mixers are typically equipped with dummy hose stations, preventing vacuum and convey hoses from contacting the mixing blade. This helps ensure that no tumbling occurs and increases the operator’s safety.
The Nutraceutical Industry requires a robust system to manage and process quality data, ensuring accuracy quickly. This system must provide precise data in a tamper-proof manner and meet the requirements set forth by DSHEA.