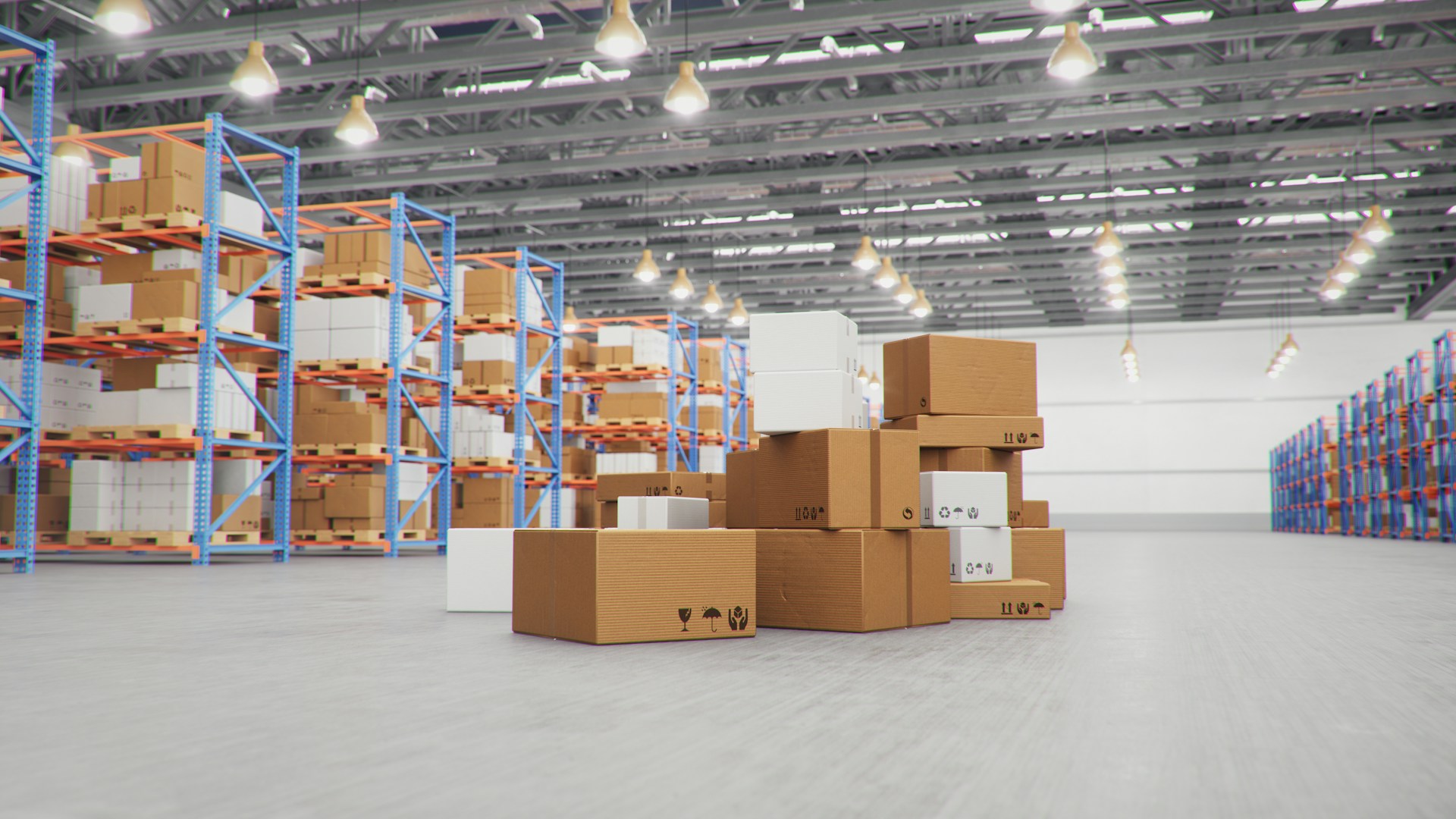
Space-Saving Secrets Every Warehouse Manager Should Know
Ever looked around your warehouse and thought, Where did all the space go? It doesn’t take much. A few off-schedule deliveries, a batch of slow-moving inventory, and suddenly every aisle feels tighter than it should. Space is money in warehousing, but too often, it’s wasted on clunky systems and poor planning.
The good news? With the right strategy and a few smart swaps, you can reclaim serious square footage without moving walls or adding new racking.
Stackable Plastic Containers
You’ve probably used them already. But are you really getting the most out of them? Stackable plastic containers beat out bulky cardboard every time when it comes to long-term storage. Why? Because they offer structure, durability, and most importantly, vertical efficiency. They’re built to stack safely without crushing the contents, which means you can finally make use of that wasted overhead space.
Unlike open bins or damaged boxes, these containers help keep things neat, labeled, and easy to find. Less mess means quicker picking and fewer errors.
Want to get even more out of them? Use standardized sizes across your storage system. This way, they nest cleanly, fit onto the same shelving, and can be moved easily in bulk. Whether you’re storing small parts or finished goods, matching containers simplify everything.
Think Vertically, Always
Floor space runs out fast. But walls? They usually have room to spare. Maximizing vertical space isn’t just about tall shelving units. It’s about how you use them. Items you rarely access? Put them up high. Fast-moving stock? Keep that in arm’s reach. Too often, valuable ground-level real estate gets eaten up by products that barely move.
If you’re using adjustable racking, check the current setup. Are the shelves spaced properly, or are you wasting inches between layers? Even a few tweaks can open up a surprising amount of room.
And don’t overlook mezzanines. If your ceiling height allows it, installing a mezzanine can give you a second floor of usable storage without expanding your footprint. It’s one of the best long-term investments for space efficiency.
Shrink Your Aisles (Slightly)
Wide aisles feel convenient. But in a warehouse, they can quietly eat up hundreds of square feet. Now, this doesn’t mean cramming everything together so tight that no one can move. But trimming aisle widths where it makes sense, especially in slow-traffic areas, can free up enough space for an extra row of racking or even a packing station.
It’s all about striking the right balance. Keep wide, clear paths where forklifts or pallet jacks operate frequently. For manual picking zones, slightly narrower aisles can be more than enough.
Before you make changes, walk the floor. Observe traffic flow. Identify pinch points. Then experiment gradually. Space efficiency shouldn’t come at the cost of safety or productivity.
Consolidate Where Possible
One of the biggest culprits of wasted space? Overstocking low-demand items or storing the same SKU across multiple locations. It might not seem like a big deal, but scattered storage adds up, and fast.
Instead of spreading things out, consolidate SKUs wherever possible. Group similar items, reduce redundancy, and stick to a logical layout. This not only saves space but also speeds up picking and reduces errors.
Cycle counts and regular inventory audits help here. You’ll spot outdated stock, identify space hogs, and make informed decisions about what to move, shrink, or phase out.
And while it’s tempting to hang onto everything “just in case,” clearing out old or obsolete inventory can be a game-changer for space. If it hasn’t moved in months, it’s not earning its keep.
Use Mobile Shelving Systems
Stationary shelving has its place, but mobile systems can double your capacity in the same footprint. These are especially effective in parts rooms, archive storage, and slower-moving inventory zones. Instead of aisles between every row, the shelves move to create access where and when it’s needed. It sounds simple, but the impact can be massive.
Just be sure the layout supports your workflow. Mobile systems don’t work for every part of a warehouse, especially high-traffic zones, but for the right area, they unlock a lot of hidden space.
Prioritize Labeling and Visibility
It might not sound like a space-saving tip, but hear this out. When items are poorly labeled or hard to identify, they often get stored in the wrong place or end up duplicated across locations. That’s how clutter grows.
Clear, consistent labeling, and ideally color-coded systems, help staff find what they need quickly and return items where they belong. Less confusion means less wasted space, fewer misplaced products, and a smoother workflow overall.
It also helps when doing stock rotations. FIFO (First In, First Out) systems rely on being able to see and access the oldest stock. If it’s buried under newer arrivals, you end up with expired or outdated inventory taking up valuable space.
Think Beyond Storage
Space-saving isn’t just about where you keep things, it’s also about how things move. Look at your packing stations. Are they set up efficiently, or are tools and materials scattered? A compact, organized packing area cuts down on movement, saves time, and reduces the need for sprawling workbenches.
The same goes for receiving. An organized inbound area keeps product flowing and avoids backup that spills into main storage. And if you’re cross-docking, make sure staging zones are clearly marked to prevent mix-ups or unnecessary storage time.
A clean, flowing layout makes the whole warehouse feel bigger, even if the footprint hasn’t changed.
Watch for Growth Traps
It’s easy to fall into the trap of expanding your footprint the moment space feels tight. But before you look for more square footage, ask whether you’re truly maximizing what you already have.
Many warehouses operate at only 70 to 80 percent efficiency without realizing it. Dead zones, poor layout, and underused vertical space are common culprits.
By improving how you use your space now, you might delay or even avoid a costly expansion. And even if you do end up expanding down the line, a more efficient system will make that space work harder from day one.
Your Warehouse Can Work Smarter
You don’t need a massive overhaul to make a big difference. A few smart changes, like switching to stackable containers, trimming down aisles, or reorganizing high shelves, can create more breathing room and streamline operations.
Every square foot you reclaim adds flexibility and cuts costs. And when your team can find what they need, move efficiently, and work safely, the whole operation runs better.
So before you add another row of racks or lease more space, take a closer look at what’s already in front of you. You might be surprised how much room you really have.